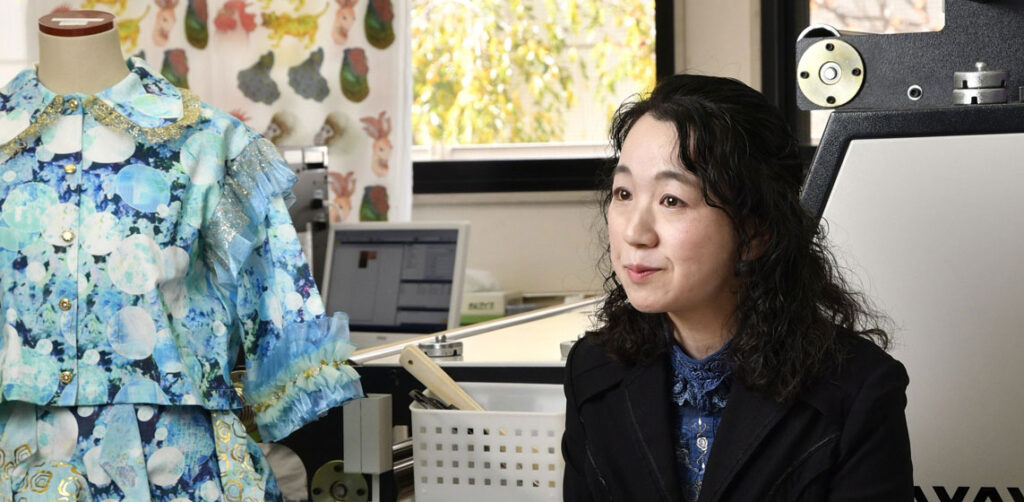
Interview with Ariha Iizuka, Full-time Lecturer at Bunka Fashion College.
Bunka Fashion College, a renowned institution in Japan known for cultivating top fashion designers, has integrated digital printing into its textile and apparel design curriculum and incorporates it in the creation of student projects. Three Mimaki inkjet printers are utilized in the digital textile lab, one of which was newly introduced this last fall. Ariha Iizuka is a full-time lecturer on Digital Textiles and CG at Bunka Fashion College. We met Ms. Iizuka in the lab and asked her about digital print education at the school.
Please tell us about the applications of digital printing and also a little about the digital textile lab
We’ve been using inkjet printers at Bunka Fashion College for about 20 years. It would seem that the lecturers who preceded me had the foresight to recognize that “the digital age is upon us”. In those days, textile courses were core, and their use by students in other programs of study was limited, but printers started being used for competition-related works, where silk-screening can’t be used, such as for photographic or hand-drawn prints.
Because the works that students make are basically one-of-a-kind, it is difficult to order such low-quantity prints from a textile dyeing factory. Another motivation for employing inkjet printers is that they allow for small-lot productions with a short turnaround, and this makes them very suitable for student-created works.
2nd year students of the Fashion Textile Department learn about textiles and practice digital printing and silk screen printing. Even with apparel majors, in our 4th-year fashion diploma course and 3rd year apparel design course, students take classes where they learn about everything, from producing CG data on a computer, to printing. And the lab is available for all Bunka Fashion College students to use and create their own works.
How are the different models utilized?
We currently have three printers in our lab: direct-on-fabric printer with reactive ink, a sublimation transfer printer, and a pigment-ink flatbed printer. The direct-on-fabric printer is a new model that was introduced in September and we started using it in October.
Basically, the particular printer used will depend on the material. We use the direct printer for cotton and silk, the sublimation transfer printer for polyester and acetate, and the pigment flatbed printer for knits and T-shirts which tend to lose their shape, and also for leather which is difficult to dye.
We’ve been able to gradually increase the number and types of machines while replacing the old ones. Initially we started with one direct printer that uses reactive ink, but many students said they wanted to print on polyester, so we added a sublimation transfer printer. In the beginning we came up with ways to make use of existing equipment, such as reusing a machine that bonds fusible interlining, but we now have a dedicated thermal transfer press. However, since also using the machine for interlining work would limit the time available to use it, we decided to next add a thermal transfer press, thereby expanding our lineup.
What are the advantages of digital printing in clothing and fashion education?
For one, there is the ability to be able to create works freely. Without such equipment, we could only produce clothing using commercially available fabrics. When it comes to contests and the like, if we didn’t have a printer, we would have to find and contract an outside printing company which not only costs money just to make a sample, but also involves a long turnaround time to complete the printed fabric.
Of course this could be considered a learning opportunity, but for students with limited time and money, it would force them to make compromises when making clothes. By having this available on campus, students can print data they have made and make their own original clothes. Thanks to such experiences, even after having entered the workforce, the idea of being able to propose printed textiles to clients is spreading.
While printing is just one element of clothing production, with digital printing, one can create originality. I believe that the experience of turning pictures into cloth will also provide an opportunity for people to discover the joy of textiles.
Seeing an image on a screen or smartphone makes it difficult to grasp size and other aspects. However, having an actual printed item is important because it allows one to experience the difference in size and colors from what can be seen on the screen. With a print in hand, we can readily see important points to consider when placing orders with venders at their place of business.
And recently, apparel companies are looking for workers with the skills needed to create data using a computer, and workers who have learned such skills through the making of printed fabrics are at an advantage. We even hear about graduates who have gained opportunities by proposing products using original patterns, even though their work is not directly related to printing.
And speaking of working with digital data, design work and virtual prototyping using 3D modeling are attracting attention. We have also started classes at Bunka Fashion College that incorporate 3D CAD (computer-aided design) and going forward, the ability to create new clothes which directly link print design and apparel design is likely to expand.
Contest Winning Works that Utilized Digital Prints
What have been your achievements in creating works utilizing digital printing?
The 2021 work of a student who won the Bunka Fashion College fashion contest design grand prize for the second year in a row is a dress that combines printing and pleating on thin organdie. The work is a sublimation transfer print of a red-based design inspired by tropical fish.
One student’s work that incorporated printed decorative parts won the Encouragement Prize of the 2022 Nagoya Fashion Contest.
Another student’s work which was selected for the final judging of the 96th Soen Award was a three-dimensional piece that used fabric printed in shades and gradations of red. The piece worn by Non, who appeared as a special guest model at Shibuya Fashion Week 2022, also incorporated digital printing. With “skin” as the theme, the shoulders of the jacket and sides and back of the jumpsuit take on a tattoo-conceptualized pattern.
Lastly, please tell us why you chose Mimaki Engineering printers, and what sort of things you would like to see in the future.
We have been using Mimaki printers for quite some time now and replaced a discontinued direct printer with the new “Tx300P-1800MkⅡ” model. There are very few entry-level direct printers that support printing on fabric widths up to 1.8 meters. The image quality that the Mimaki printer provides is excellent and the colors are uniform and consistent. Operation is also stable, and you can feel the evolution of the machine. We are grateful for things such as how Mimaki supplies consumables and handles product maintenance, as well as the support system that they have in place.
The flatbed model which we continue to use has been discontinued and is no longer supported, but it is a convenient machine to use, so we would really like to see its successor developed. DTF (direct-to-film) printers, which can handle any kind of fabric, are also drawing attention, and we are also thinking about adding one of these to our lineup.