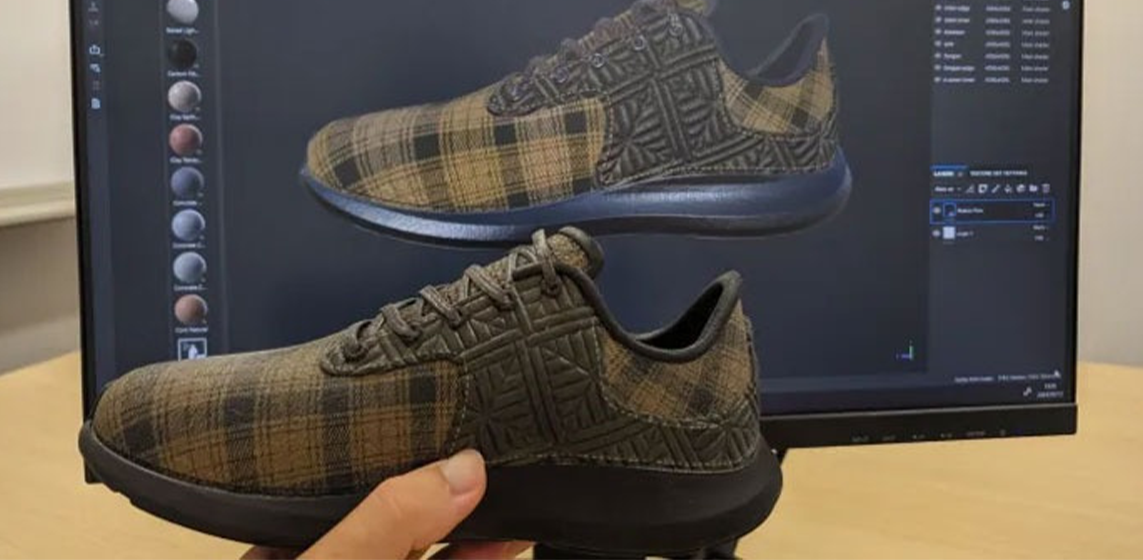
- Developing prototypes for footwear brands previously took over a month from order placement to delivery, slowing the design process and delaying feedback. With the Mimaki 3DUJ-553, this timeline has been reduced to just one to two days, enabling rapid design iterations. This accelerated workflow allows designers to make modifications and produce multiple prototypes quickly, resulting in more refined and innovative product development.
Throughout the footwear design process, prototypes are a critical step in bringing shoes from concept to reality – but until now the step has been slow and costly. That’s where Mimaki comes in. Launched in 1975, the Japan-based digital printer manufacturer has become an innovator in helping leading footwear brands expedite their design process with full-colour 3D printing.
The samples created by Mimaki are sturdy, purpose-built prototypes, featuring up to 10 million different colours and express a variety of textures from the Adobe Substance texture library. From shoelaces to the outer sole, the prototypes help brands get a hyper-realistic mock-up for their next big launch.
Importantly, the realism does not come at the cost of speed. The Mimaki 3DUJ-553 full-colour 3D printer can print a full-sized footwear prototype in under one day, making it easy for brands to assess their prototype, make changes and create another 3D model, ultimately saving brands months during the often long design process.
Michael Sickels, 3D specialist of global marketing group at Mimaki Engineering, sat down with Fairchild Studios to explain the process behind printing 3D prototypes, how the company is expediting the typical timeline of designing, the impact of 3D printing beyond just the footwear industry and more.
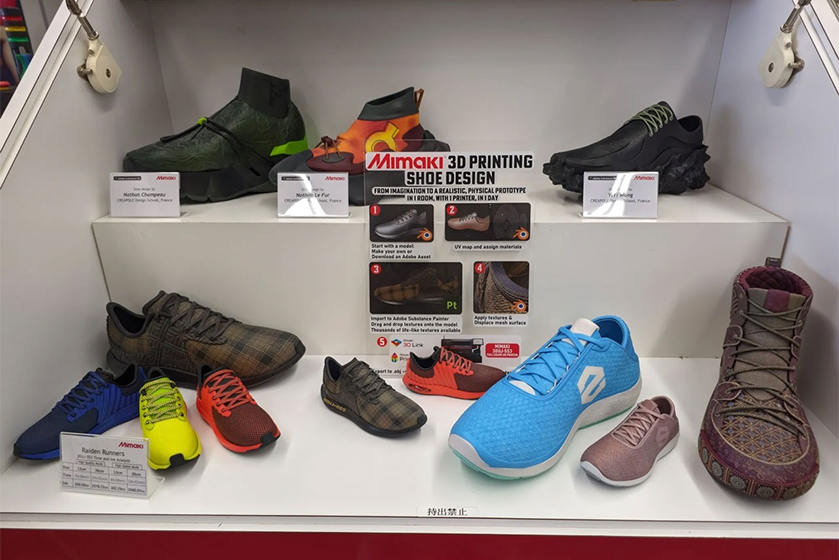
Fairchild Studio: In your own words, how would you describe Mimaki?
Michael Sickels: The Mimaki Group is a development-driven group of companies that provide integrated services through the development, manufacturing, sales and maintenance of products such as industrial inkjet printers, cutting plotters and inks. Our development history began in 1987 with our first drafting plotter.
In 1996, we debuted our first inkjet printer and now have models applying ink down to 3 picoliters. To put that in perspective, there are 1 trillion picoliters in a liter — the human eye cannot see it.
In 2017, Mimaki took all those colourful years of high-performance inkjet development and brought it to 3D. The 3DUJ-553, an industrial full-colour 3D inkjet printer, was born. Although this was our first 3D printer, we were able to leverage our extensive experience with ink jetting to bring unparalleled colour and detail expression to 3D printing.
Fairchild Studio: In what ways is Mimaki’s full-colour 3D printer an asset to footwear designers and students throughout the design process?
M.S.: Mimaki’s full-colour 3D printers add value to the design process in the form of speed, creativity and ease of integration. Having the Mimaki 3DUJ-553 in the design room or design school removes the need to order early, nonfunctional prototypes to be made at a factory. That cuts months from the design process.
The 3DUJ-553 can print in 10 million colours and can print shapes and patterns that are difficult to conventionally produce. Lastly, the 3DUJ-553 can print 3D models made using industry-standard software whether it is Adobe Substance, Rhino, ZBrush, Modo or Autodesk.
No significant changes are required to your current workflow, you are gaining the ability to turn your wonderful, detailed designs into ones you can hold and feel in your hands.
Fairchild Studio: How does the ability to print highly realistic prototypes within a day impact the typical timeline of a footwear design project?
M.S.: Traditionally, footwear designers send tech packs to factories — usually in Asia — to have prototypes made. From order to prototype delivery, it can take easily over a month before a physical prototype is in the hands of a designer for expert appraisal. If there are any major changes, another prototype needs to be ordered, which will eat up more of that already scarce time in the product development cycle.
Imagine this: You install a full-colour 3D printer in the design room and rapidly produce the prototypes in-house. The Mimaki 3DUJ-553 can print a visually realistic men’s size 9 shoe in under a day. Footwear designers can then appraise the print, make changes to the 3D model data and then print again. A process that normally takes months can be condensed into a few weeks, with all the magic happening in your own workplace.
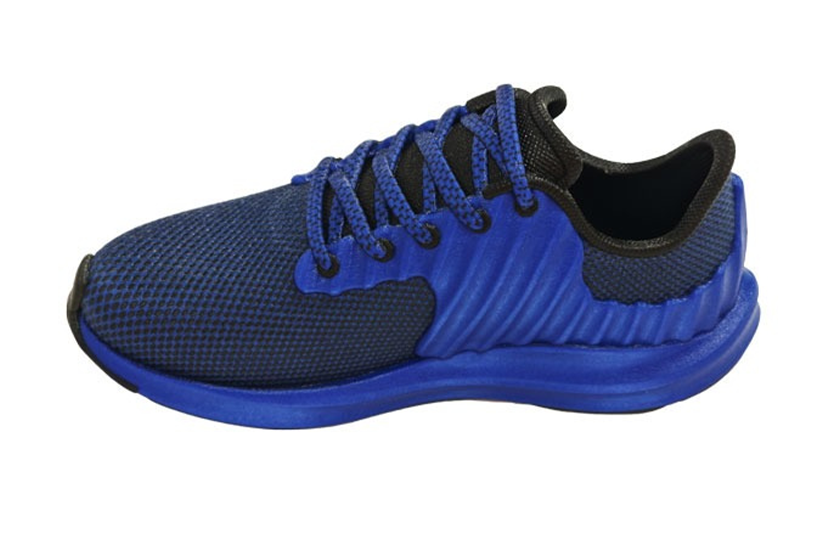
Fairchild Studio: How does Mimaki’s integration with industry-standard software like Adobe Substance enhance the functionality and user experience?
M.S.: There are two areas where functionality and the user experience are enhanced. Firstly, full-colour printing on the Mimaki 3DUJ-553 is compatible with all the major 3D data formats that include colour — .obj, .ply, .wrl and .3mf. A designer can continue using their favorite 3D modeling software. Once the printer is installed and basic printer training is given, designers can begin full-colour 3D printing of their designs quickly.
Secondly, the 3DUJ-553 can express your designs in a life-like quality. Not only can the printer express 10 million colours (including clear), but each layer of the model can be printed as thin as 20 micrometers. Imagine slicing your design into 20-micrometer layers from top to bottom, that is how fine the detail can get. Thanks to these features, the denim, mesh, leather or nylon you have on your shoe design will look like the real thing on your physical 3D print.
Adobe Substance, which is gaining wide adoption in the industry, is a great way to capitalize on this. Adobe Substance gives designers access to a library of thousands of realistic materials — even allowing you to scan your own — which can be dragged and dropped onto different parts of the footwear 3D model. The designer can then print the design and assess a visually realistic physical prototype. Imagination is the only limit.
Fairchild Studio: How do the features of the Mimaki 3D printer align with the specific needs of footwear designers looking to enhance creativity and innovation in their design process?
M.S.: Mimaki full-colour 3D printing gives footwear designers access to quality rapid prototyping with confidence without the need for major changes to workflow. These benefits enhance creativity.
To illustrate this, imagine a designer thinking: “I haven’t tried this material/style/colour before. It might not work but I’d like to see it. With a Mimaki 3DUJ-553, why not give it a try? You can have the life-like prototype in your hand in a day or two”. In this way, the convenience and quality factor increase a designer’s creative freedom.
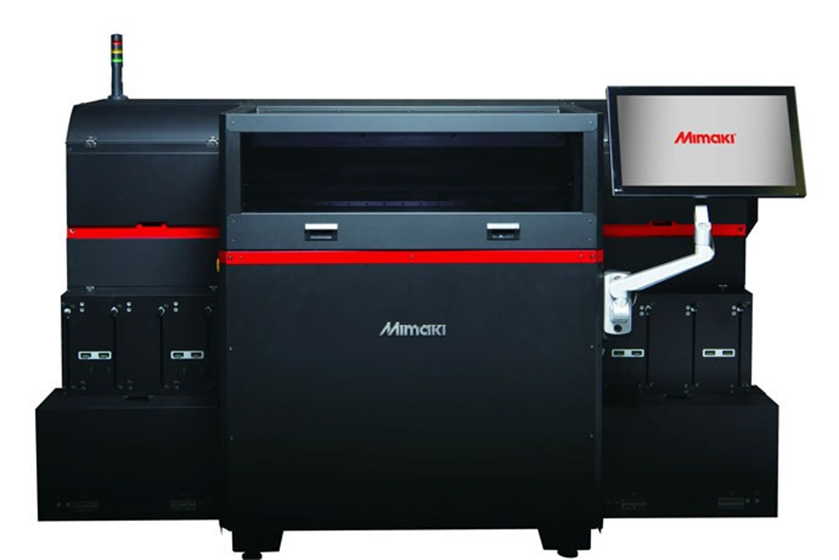
Fairchild Studio: Beyond footwear, how else is the company’s 3D printer able to create valuable prototypes in the merchandise and accessories market?
M.S.: The 3DUJ-553 works well with 3D CAD, CG and 3D scan software. Professionals in various industries have been able to apply our 3D technology to their specialized needs. For example, the colour expression and precision of our 3D printers have found a home in the figurine and scale model industries.
Our printers are being used to prototype figure designs and even produce figures or models for sale to end customers. Our printers also work well with 3D scan data. A few companies have been using special 3D scanning equipment to scan people, pets and other memorabilia for full-colour printing on the 3DUJ-553. Drones have even been used to scan buildings and towns to create 3D data to be later printed.
In the medical industry, we have some customers using the 3DUJ-553 to print highly detailed and accurate medical models. CT and MRI data can be used in this way. Architectural and construction firms have also shown interest in full-colour 3D printing for analysis of designs as well as for use in presentations to customers and communities.
In these ways, a broad range of industries are finding value in our technology and I truly want our full-colour 3D printing (and additive manufacturing as a whole) to become common knowledge. I want more people to know that these amazing things are possible today.
Fairchild Studio: How do you see the future of footwear design evolving through innovations and speed of 3D printing and prototyping?
M.S.: 3D modeling is going to increasingly become the way to design footwear. It offers designers so much more convenience and freedom in their creativity. Given that 3D printing goes hand in hand with 3D modeling and that 3D printers have achieved a high level of print quality, it is only natural that there will be increased adoption.
I have been told by several designers that nothing beats having a prototype that you can hold and feel in your hands. Physical prototypes are not going anywhere. 3D modeling and 3D printing will shorten the time from idea to design as well as give designers more flexibility. For these reasons, I believe that 3D is going to continue to revolutionize footwear design going forward.
Mimaki will have a booth at the Formnext convention in Frankfurt, Germany on November 19-22. Everyone is invited to stop by to check out the full-colour footwear samples and ask any questions in-person!