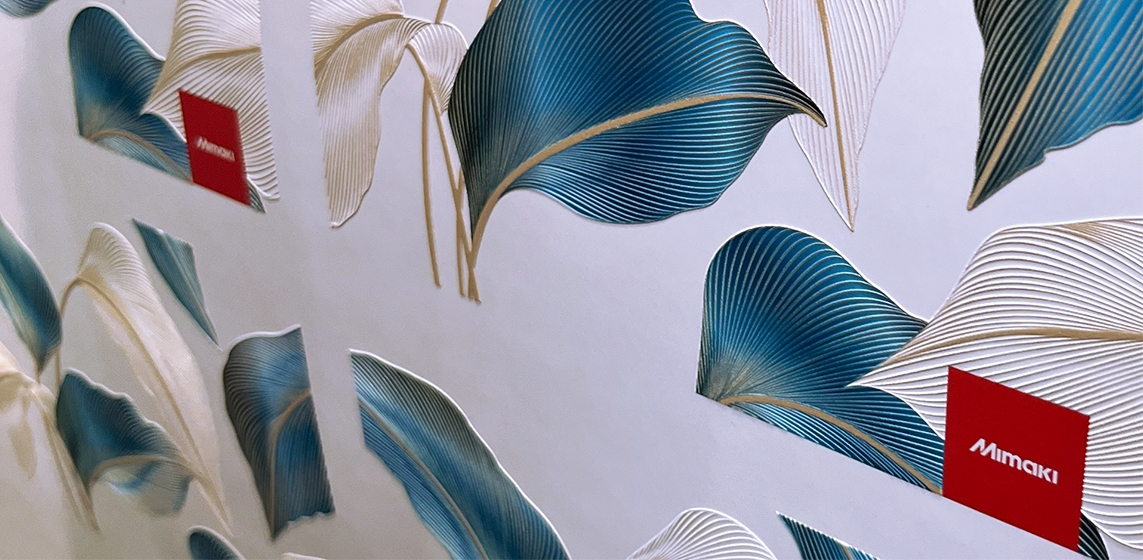
By Marc Verbeem, Supervisor Product Management, Mimaki Europe
Since launching the first UV printer with white ink in 2004, Mimaki has consistently pioneered the development of innovative UV-LED technology. Our range of UV printers grew as recently as September last year, with the introduction of the UCJV330-160 and the UJV100-160Plus. In this blog, Marc Verbeem will detail how using UV-LED printing, you are not only upgrading the quality of the print but also meeting sustainability targets the entire industry is striving towards.
Better, faster and for longer
Striking, high-resolution prints are naturally the number one priority for any printer in any industry, and a switch to UV can not only elevate your designs but also expand your printing possibilities. Our new printers add gloss, matte, or other textured finishes during the printing process through layered printing functions, giving designs an almost 3D effect. As well as this, UV inks dry instantly, without any smudging or colour bleeding, leaving you with a print that not only boasts vivid, photo-realistic image quality but is ready for use immediately.
The removal of the drying process drastically increases the production speed, something that is crucial when keeping up with increased demand. According to Keypoint Intelligence’s research, over 60% of large format print jobs in the sign industry require turnaround times of less than 24 hours.[1]. Having a UV printer will help supply keep up with demand, and also save money in investing in additional printers to do so.
UV printing is incredibly versatile, with the ability to be applied to a wide range of traditionally hard-to-print surfaces, such as paper, plastic, glass, metal, wood and more. This is a massive advantage in the luxury packaging industry, where bottles and containers can be irregular shapes and be made of a variety of materials. Another advantage of UV, in comparison to traditional methods, is the durability of the inks. UV inks are more resistant to scratches, fading and abrasion, which makes them particularly suitable for outdoor applications, for example, car wrapping.
Leaving your mark in print, not on the planet
While the immediate focus of printers is providing high quality prints to customers, there is an underlying long-term goal to make the industry more sustainable. By using UV-LED, you can make significant reductions in your waste and carbon emissions, while improving the quality of your print.
As mentioned previously, there is no curing and drying process with UV, which subsequently means there is no accompanying curing heater. By removing this part of the process, you can reduce energy consumption by 90%, thus significantly reducing your carbon footprint.
Another way that UV-LED printing is more sustainable is through use of waterless inks. There is a myth that water-based inks are better for the environment, however, health and safety data show that 35% of chemical make up in latex inks, for example, are harmful and toxic to humans and the environment. The drying process consumes more power because evaporating the remaining 65% of water requires significant heat. Water is the most valuable resource on the planet, the less we use the better and so using waterless inks is a fantastic way to reduce the amount of water we use.
Not only does UV-LED printing use less water and energy, but it also produces less waste. Traditional thermal print heads for latex printing need replacing regularly, however, UV printing uses Piezo electric print heads which have much longer durability. These print heads do not suffer thermal stress like thermal print heads do, which means they experience less degradation and also provide a more stable print quality. Over the lifetime of the printer (approximately five to seven years if well maintained), with a Piezo print head, you will only go through two to three print heads. When you compare this to thermal print heads, which you may need to replace over fifty times in a two-year period, UV-LED will not only save on money spent on print heads but also significantly reduce waste.
[1] Source: Keypoint Intelligence: Global printed signage market